Voorpagina
Voor €10,- per jaar geniet je als lid van J.F.V. Grotius onder andere van gratis borrels, kantoorbezoeken, lezingen en reizen!Lid worden 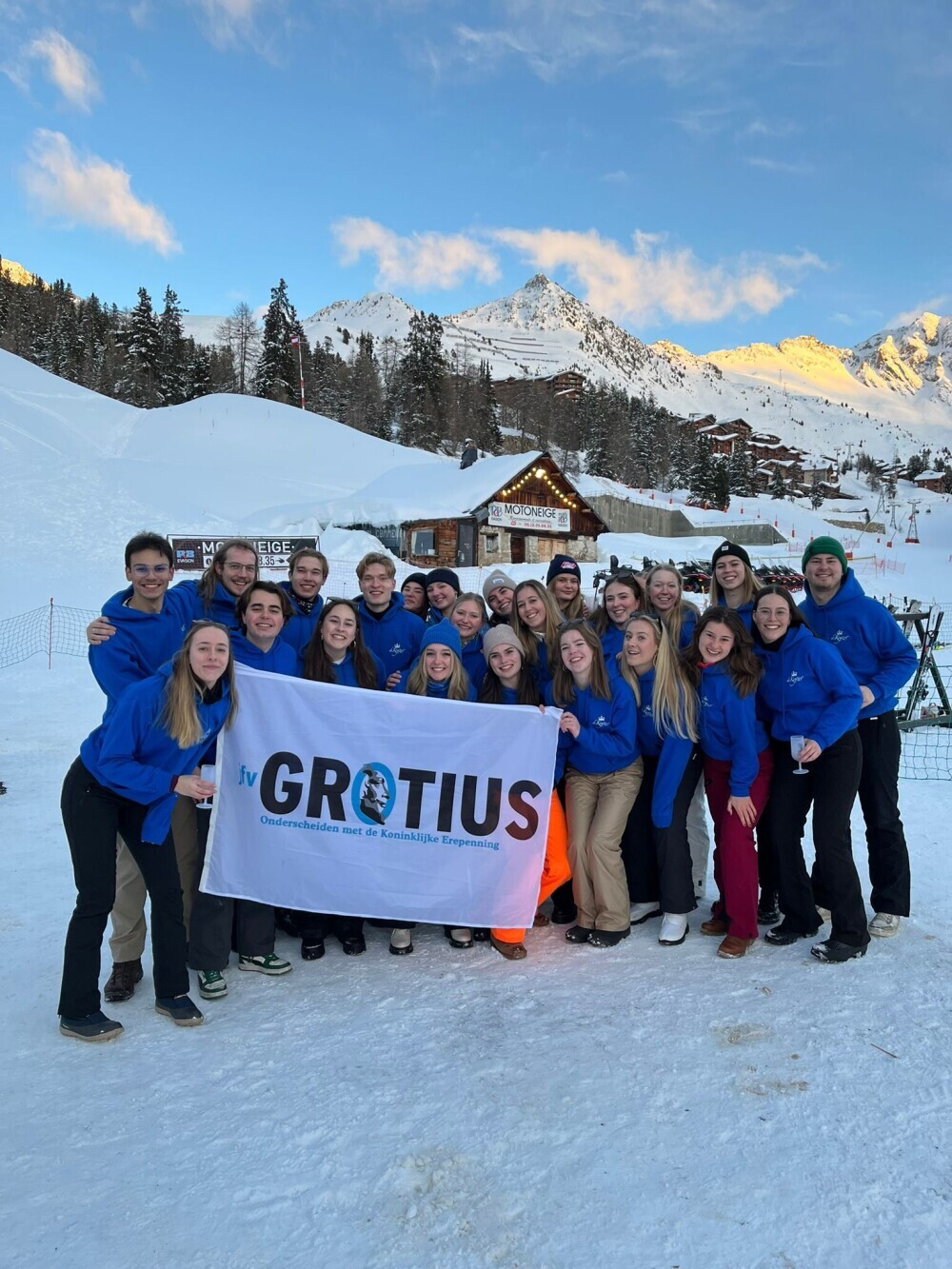
Leden van J.F.V. Grotius profiteren van 5% korting op studieboeken! Boekenverkoop 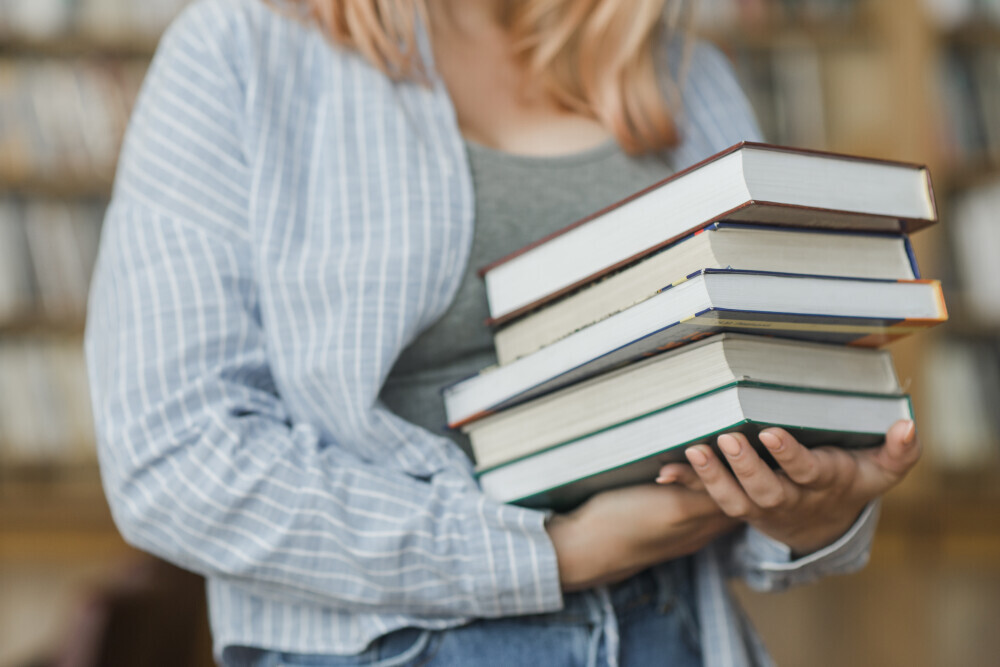
Introductieweekend
26 tot 28 september 2025
Bekijken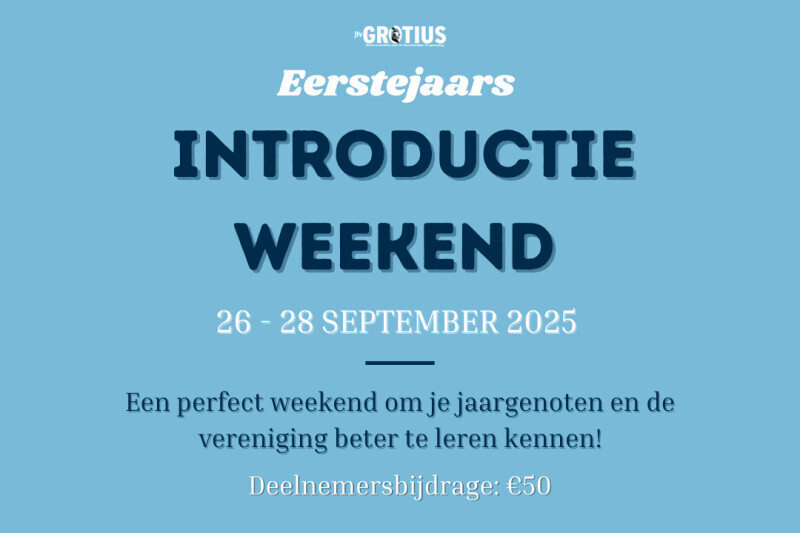
Kleine reis Wenen
08 juli 2025
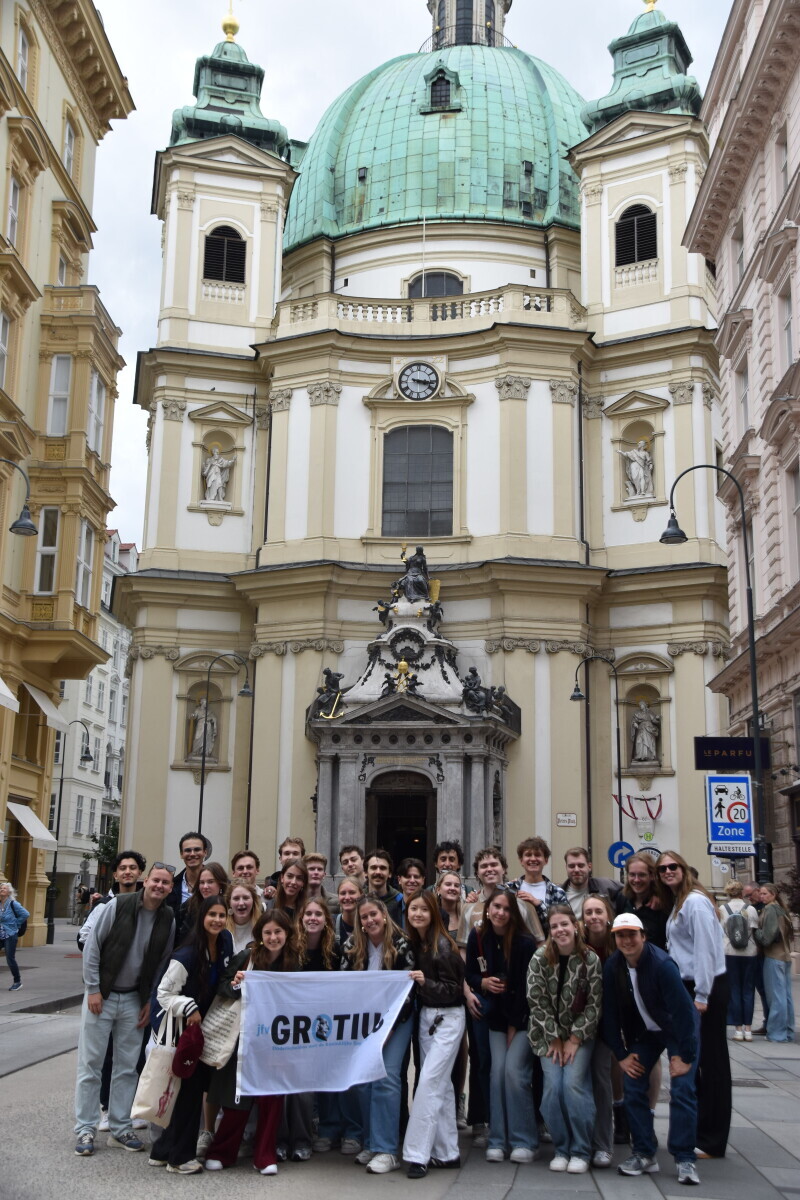
Koffieshaker borrel
03 juli 2025
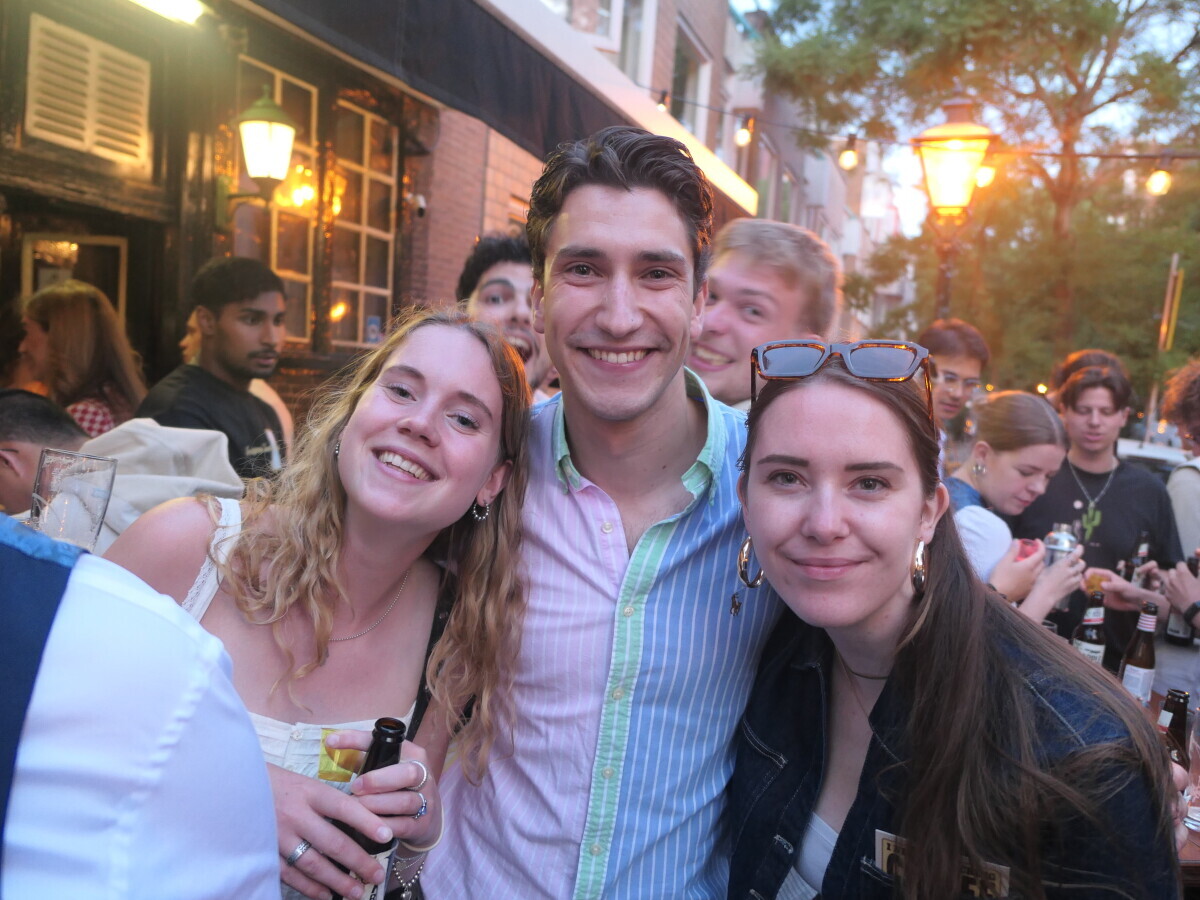
Eerstejaarstrip Groningen
26 juni 2025
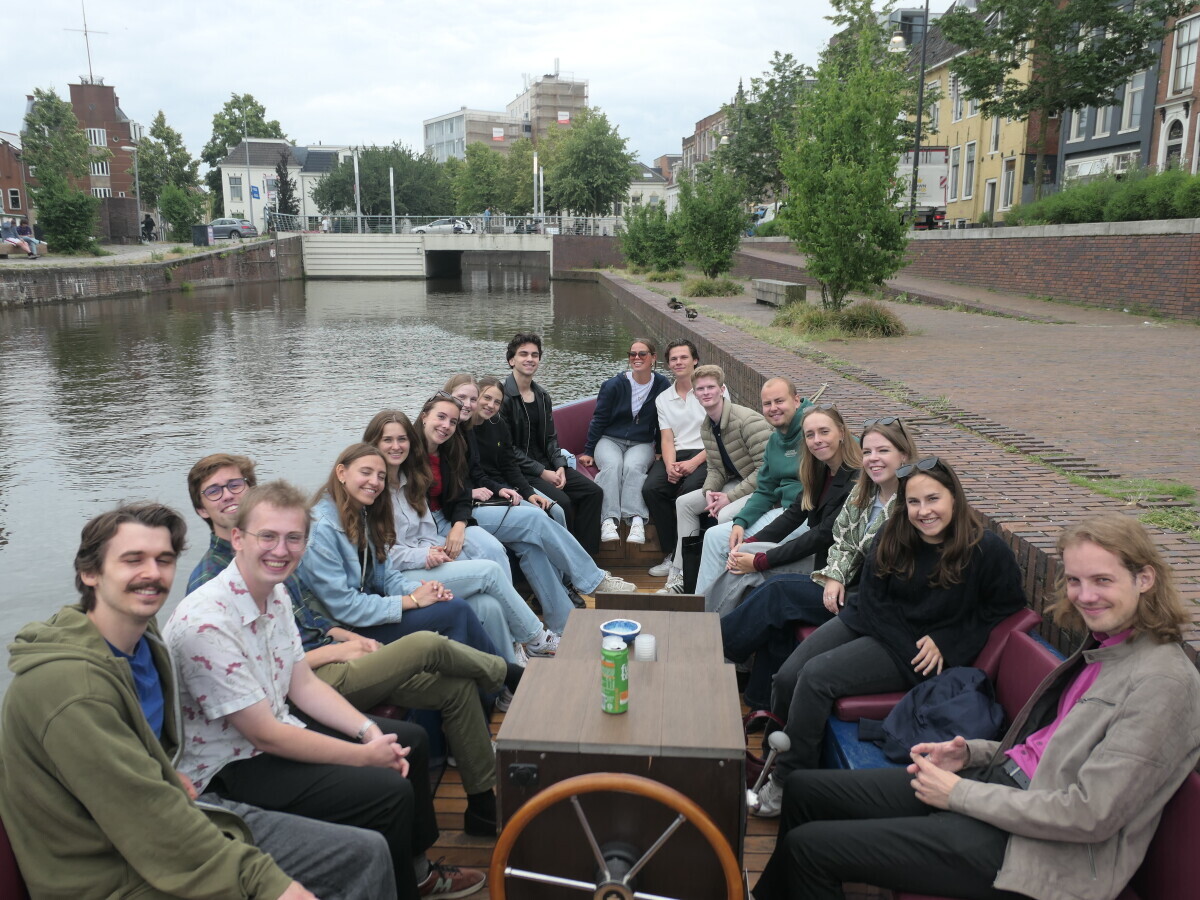
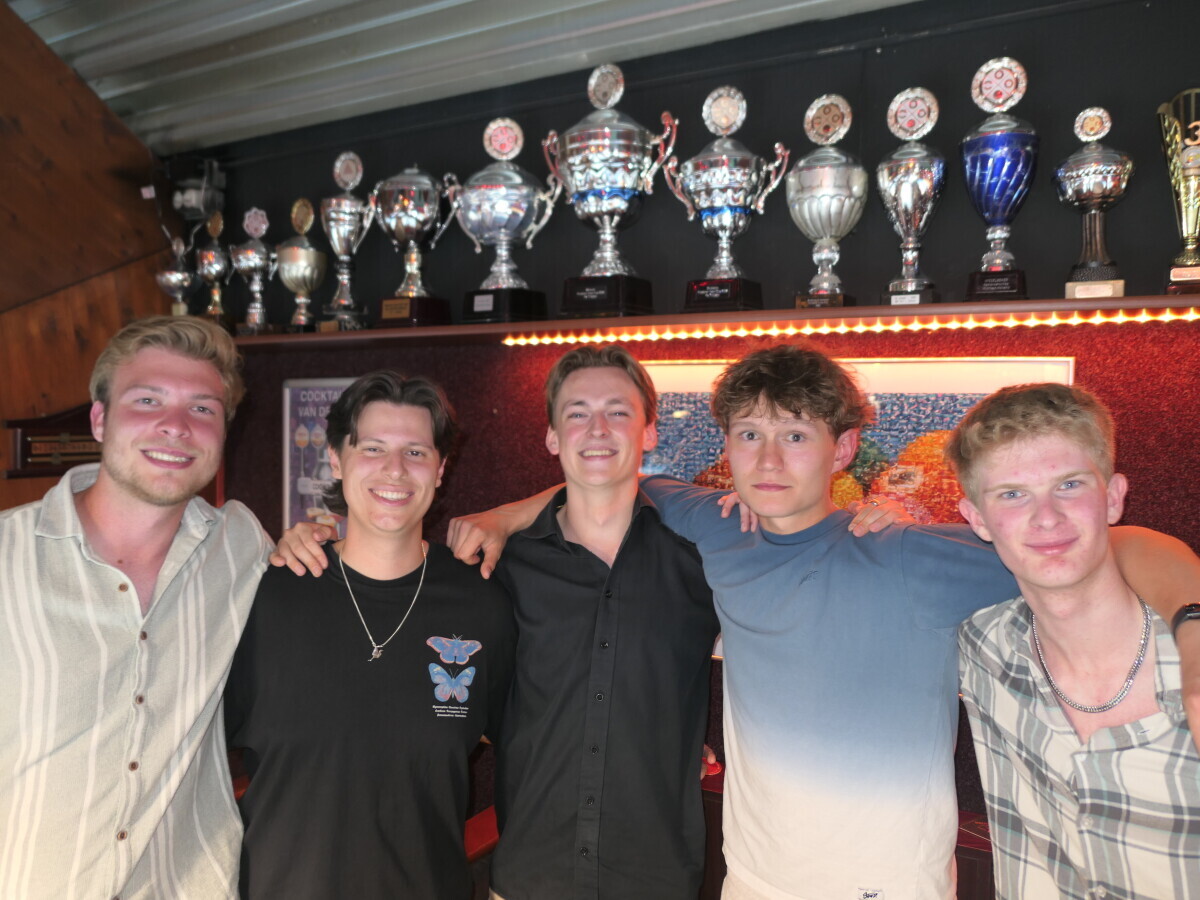
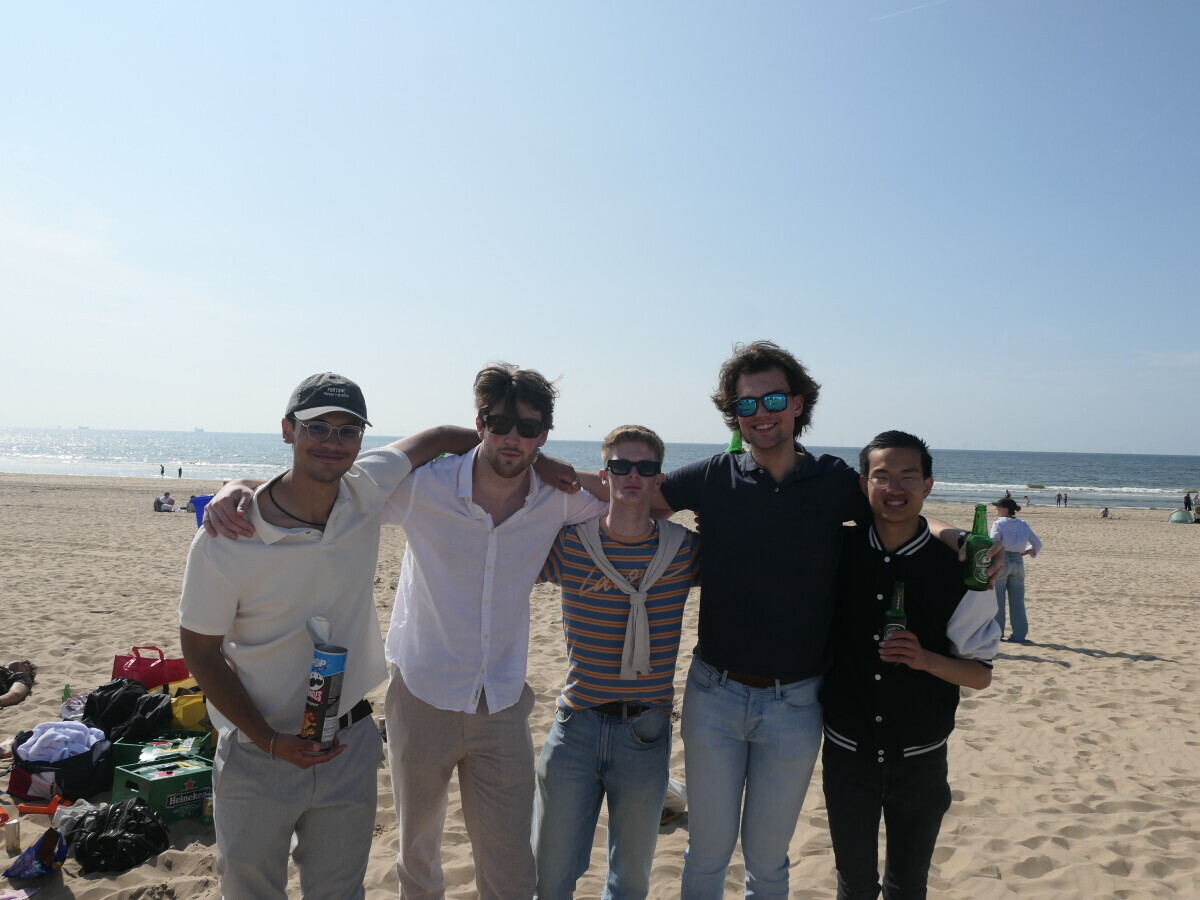
Commissiebedankdag
12 juni 2025
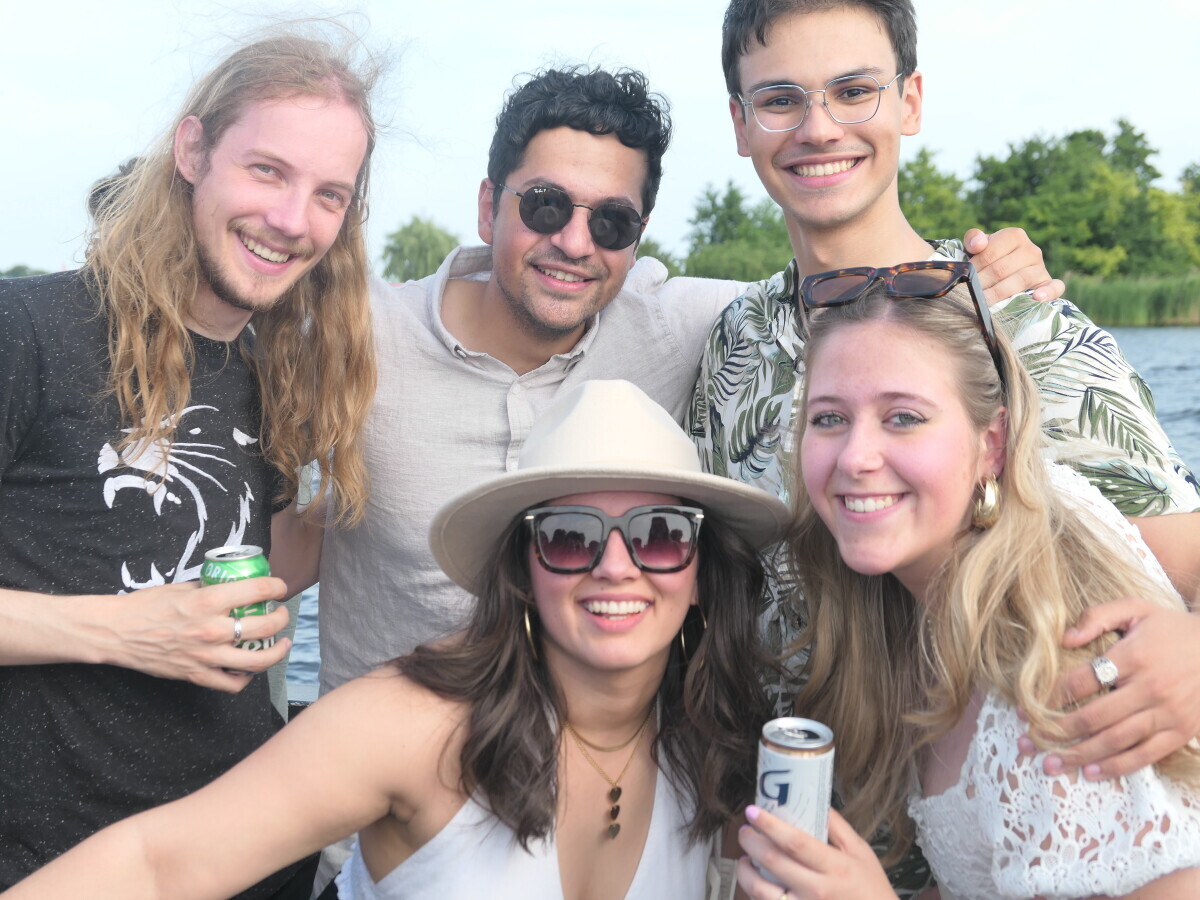